INTRODUCTION TO MECHANISM:
A mechanism is a device designed to transform input forces and movement into a desired set of output forces and movement. Mechanism generally consists of moving components such as gears and gear trains, belt and chain drives, cam and follower mechanisms, and linkages as well as friction devices such as brakes and clutches, and structural components such as the frame, fasteners, bearings, springs, lubricants, and seals, as well as a variety of specialized machine elements such as splines, pins and keys.
The German scientist Reuleaux provides the definition “a machine is a combination of resistant bodies so arranged that by their means the mechanical forces of nature can be compelled to do work accompanied by certain determinate motion”. In this context, his use of machine is generally interpreted to mean mechanism.
The combination of force and movement defines power, and a mechanism is designed to manage power in order to achieve a desired set of forces and movement.
A mechanism is usually a piece of a larger process or mechanical system. Sometimes as entire machine may be referred to as a mechanism.
Examples: The steering mechanism in a car, or the winding mechanism of a wristwatch.
1.2 TYPES OF MECHANISM:
From the times of Archimedes through the Renaissance, the mechanisms were considered to be constructed from simple machines, such as the lever, pulley, screw, wheel and axle, wedge and inclined plane. It was Reuleaux who focussed on bodies, called links, and the connections between these bodies called kinematic pairs, or joints.
In order to use geometry to study the movements of a mechanism, its links are modelled as rigid bodies. This means distances between points in a link are assumed to be unchanged as the mechanism moves, that is the link does not flex. Thus, the relative movement between points in two connected links is considered to result from the kinematic pair that joins them.
Kinematic pairs, or joints, are considered to provide ideal constrains between two links, such as the constraints of a single point for pure rotation, or the constraint of a line for pure sliding, as well as pure rolling without slipping and point contact with slipping. A mechanism is modelled as an assembly of rigid links and kinematic pairs.
1.3 KINEMATIC PAIRS:
Reuleaux called the ideal connections between links kinematic pairs. He distinguished between higher pairs which were said to have line contact between the two links and lower pairs that have area contact between the links. J.Phillips shows that there are many ways to construct pairs that do not fit this simple.
1.3.1 Lower Pair: A lower pair is an ideal joint that has surface contact between the pair of elements. We have the following cases:
- A revolute pair, or hinged joint, requires a line in the moving body to remain co-linear with a line in the fixed body, and a plane perpendicular to this line in moving body maintain contact with a similar perpendicular plane in the fixe body. This imposes five constrains on the relative movement of the links, which therefore has one degree of freedom
- A prismatic joint, or slider, requires that a line in the moving body remain co-linear with a line in the fixed body, and a plane parallel to this line in the moving body maintain contact with a similar parallel plane in the fixed body. This imposes five constraints on the relative movement of the links, which therefore has one degree of freedom.
- A cylindrical joint requires that a line in the moving body remain co-linear with a line in the fixed body. It is a combination of a revolute joint and a sliding joint. This joint has two degree of freedom.
- A spherical joint, or ball joint, requires that a point in the moving body maintain contact with a point in the fixed body. This joint has three degrees of freedom.
- A planar joint requires that a plane in the moving body maintain contact with a plane in fixed body. This joint has three degree of freedom.
- A screw joint, or helical joint, has only one degree of freedom because the sliding and rotational motions are related by the helix angle of the thread.
1.3.2 Higher Pair: Generally, a higher pair is a constraint that requires a line or point of contact between the element surfaces.
For example, the contact between a cam and its follower is a higher pair called a cam joint. Similarly, the contact between the involute curves that from the meshing teeth of two gears are cam joints.
1.4 Planar Mechanism:
A planar mechanism is a mechanical system that is constrained so the trajectories of points in all the bodies of a system lie on planes parallel to a ground plane. The rotational axes of hinged joints that connect the bodies in the system are perpendicular to this ground plane.
1.5 Spherical Mechanism:
A spherical mechanism is a mechanical system in which the bodies move in a way that the trajectories of point in the system lie on concentric spheres. The rotational axes of hinged joints that connect the bodies in the system pass through the center of these spheres.
1.6 Spatial Mechanism:
A spatial mechanism is a mechanical system that has at least one body that moves in a way that its point trajectories are general space curves. The rotational axes of hinged joints that connect the bodies in the system from lines in space that do not intersect and have distinct common normal.
1.7 Cam and Follower Mechanism:
A cam and follower is formed by the direct contact of two specially shaped links. The driving link is called the cam(also see cam shaft) and the link that is driven through the direct contact of their surfaces is called the follower. The shape of the contacting surfaces of the cam and follower determines the movement of the mechanism. In general a cam follower mechanism’s energy is transferred from cam to follower. The cam shaft is rotated and, according to the cam profile, the follower moves up and down. Now slightly different types of eccentric cam followers are also available in which energy is transferred from the follower to the cam. The main benefit of this type of cam follower mechanism is that the follower moves a little bit and helps to rotate the cam 6 times more circumference length with 70% force.
1.8 Flexure Mechanism:
A flexure mechanism consisted of a series of rigid bodies connected by compliant elements (flexure bearing also known as flexure joint) that is designed to produce a geometrically well-defined motion upon application of a force.
LITERATURE REVIEW:
Before commencing any design work it is useful to see what is already being done by others in the same field. As mentioned in the introduction Geneva mechanism , is also called Geneva stop, one of the most commonly used device for producing intermittent rotary motion, characterizes by alternative periods of motion and rest with no reversal in direction. It is also used in indexing.
For a background for the elimination of the shock loading at beginning and end of the motion a research paper was reviewed. The paper “DEVELOPMENT OF A NEW GENEVA MECHANISM WITH IMPROVED KINEMATIC CHARACTERISTICS” by R.G.Fenton, Y.Zhang and J.Xu. The paper discus about the reduction of the peak acceleration values and peak velocity values, and making the new mechanism well suited for high speed application. And furthermore it discuss about improvement to the designed of a curve slotted Geneva wheel, by introducing an offset to the curved slot. Another research paper “TWO STATION GENEVA MECHANISMS” Y.Zhang, R.G.Fenton and J.Xu provided information about two different methods for reducing the size of the slot and change its shape in order to make the mechanism feasible foe practical application. The reduction of the slot size is achieved either by choosing appropriate value for α. Which are highly related to this project because with this information we reduce the usage of work and time.
Another text was found from the books “CLASSIFICATION AND MODERN MECHANISMS FOR ENGINEERS AND INVENTORS” by Jensen and “THEORY OF MACHINES AND MECHANISM” by E.Bautista give the information about the description and motion characteristics. The motion characteristics give the rotation of the Geneva wheel which is the major part for the production of feed.
Another text that was found from the book “GENEVA MECHANISM” by Bin Zhang provides a major information about the lengths and dimensions to the Geneva wheel which is used for the construction of the Geneva wheel.
Complete Solution
Chat with our Experts
Want to contact us directly? No Problem. We are always here for you
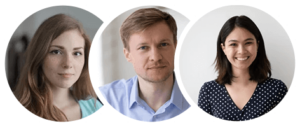
Get Online
Assignment Help Services