INTRODUCTION:
Engineering design is a process of methodical series of steps for creating function products and processes. In which Computer Aided Design (CAD) helps in creating computer models generated by geometrical parameters appearing as three-dimensional or two-dimensional parts which can be altered easily. Computer Aided Manufacturing is a process that uses models from CAD software generating tool paths to drive and turn design into physical parts. The challenges faced by the designer firstly, is to attract and retain customers in the market. Secondly, they need to maintain the competitive levels in the marketplace to increase the share and profitability. Thirdly, they should meet the requirements of diverse committees and government existing within global supply chains.
Few other designs supporting software’s include CREO, CATIA, SOLIDWORKS, etc. CREO listed as a design feature based solid modelling software helps in product design for discrete manufacturers. It is the feature based modelling in which every feature is individually described and then integrated into the part. The design procedure includes creating a model, viewing it, assembling parts as required and then to be generated. It’s the software application within CAD/CAM/CAE along with other similar products in the market. The capabilities of this feature include:
• 3D Solid Modelling
• Direct Modelling
• Robust Assembly Modelling
• Technical Surfacing
• Freestyle Surfacing
• Sheet metal Modelling
• Weld Modelling and Structural framework design
• Analysis Features
• Library of parts, features, tools
• Integrated NC capabilities
Features that can be accomplished during part designing:
1) Designing the feature base
2) Defining and redefining construction features
3) Modifying the dimensional values of part features
4) Embedding design intent using tolerance specifications into the model
5) Pictorial and shaded views of the component are created
6) Creating part families
7) Mass properties analysis and clearance checks
8) Part, feature, layer and other model information
9) Measuring and calculating model features
10) Detail drawings of part is created.
2. MOULDING
Moulding is the manufacturing process used to shape liquids or raw materials using a firm frame called Mould. Mould can be made by itself using a pattern or model of the finalised object. It is a hollowed-out block filled with a liquid material such as glass, metal, ceramic material or plastic acting as a counterpart to a cast. Different types of moulding include:
• Blow Moulding
• Compression Moulding
• Extrusion Moulding
• Powder metallurgy
• Injection Moulding
• Matrix Moulding
• Transfer Moulding
• Spin Casting
• Reaction Injection Moulding
• Rotational Moulding
2.1. INJECTION MOULDING
Injection Moulding is the manufacturing process of producing parts by injecting materials into the mould. Heated molten material is forced into the mould cavity under pressure which ranges from 5000 to 20000psi. Due to such high pressures moulds must be clamped during injection and cooling. Cavity acts as negative part being produced which is filled with plastic, heated and then cooled where plastic becomes solid material resulting in finished positive component. Low tolerances can be accomplished with proper selection of material, part design and mould design. To exhibit much more better-quality products few recommended considerations are as follows:
a) Wall thickness must be uniform
b) Less material requirement and curing time can be possible with thin walls
c) Wrapping is less in contour parts than flat parts
d) Proper venting removes trapped air from mould
e) Fillets to be used as a base of ribs or bosses
ADVANTAGES:
• Scrap loss is in lower rates
• Production rates are high and fast
• Wide range of materials can be processed
• Low man force (Labour requirement is low)
• Flexibility with design
DISADVANTAGES:
• Initial tooling cost is high
• Part design restrictions
• Knowing accurate costing is difficult
• Designing of part for effective moulding is required
Few of its applications include:
i. Packaging
ii. Bottle Caps
iii. Automotive Parts
iv. Gears
v. Storage Containers
vi. Household Goods
3. MACHINING
Moulds are built through two main methods:
i. Standard machining and
ii. Electric Discharge Machining.
Standard Machining, in its conventional form, has historically been the method of building injection moulds. With technological development, CNC machining became the predominant means of making more complex moulds with more accurate mould details in less time than traditional methods.
The electrical discharge machining (EDM) or spark erosion process has become widely used in mould making. As well as allowing the formation of shapes which are difficult to machine, the process allows pre-hardened moulds to be shaped so that no heat treatment is required. Changes to a hardened mould by conventional drilling and milling normally require annealing to soften the steel, followed by heat treatment to harden it again. EDM is a simple process in which a shaped electrode, usually made of copper or graphite, is very slowly lowered onto the mould surface (over a period of many hours), which is immersed in paraffin oil. A voltage applied between tool and mould causes spark erosion of the mould surface in the inverse shape of the electrode.
3.1 NC MACHINING
This kind of machining is the programmable automation controlled by numbers, letters and symbols. Using these we can form a programme of instructions for work part or job. When job changes programme of instructions can be changed. This flexibility is possible with only NC machining. Numerical control should be considered as a possible mode of controlling the operation for any production, possessing the following characteristics:
i. Similar work parts in terms of raw material (e.g. metal shock for machining)
ii. Work parts produced in various sizes and geometries.
iii. Work parts produced in batches of small to medium size quantities.
Many machining jobs meet these conditions. The machined work parts are metal, they are specified in many different sizes and shapes and most machined parts produced in the industry today are made in small to medium sizes. An operational numerical control system consists of the following three basic components:
1. Program of instructions.
2. Controller unit, also called machine tool unit.
3. Machine tool or other controlled process.
SPECIFICATIONS OF THE PART:
Name of the component: TV Remote Panel
Uses of the component: Acts as protective outer layer body for the electric devices.
4. PROCESS PLANNING:
Planning the entire process for making a product through injection moulding is called Process Planning. Equipment, tooling, processes and the sequencing of operations required to transform a chosen raw material into a finished product.
The steps involved in planning a process are:
Step1: selection of part
Step 2: selection of material
Step3: Designing of model part in Creo-parametric
Step4: Designing of mould and cavity for the designed part.
Step5: Performing NC Milling of the designed core and cavity.
Step6: passing of molten liquid into the mould.
Complete Solution
Chat with our Experts
Want to contact us directly? No Problem. We are always here for you
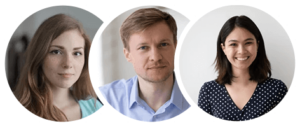
Get Online
Assignment Help Services