MOTIVATION
Robotics presently stands as one of the greatest accomplishments in the history of mankind. It influences the attempts to produce an artificial intelligent system imitating the natural intelligence of humans and thus making tasks easier. In recent years, the advancement and development of robotics has been made accessible to general public.
Our team has always been interested in doing robotic applications based projects. Our motivation behind choosing this domain was primarily an interest in undertaking a challenging area of research. With the advent of modern technology and evolution in robotics, the field has been developing exceedingly over the last few decades, and is sure to develop in the future as well. The opportunity to learn and innovate in this exciting field of research was appealing. As a part of our common interest we did our mini and major projects related to robotic applications that would make human life much safe and easier.
Now a days safety concern is one of the major applications in artificial intelligence. Our major project concerns to one such application focused mainly on the coal mine industry. The safety of workers is always a primary consideration in any form of coal mining. Coal mining deep underground involves a higher safety risk than coal mined in opencast pits, due primarily to problems associated with mine ventilation, the potential for mining collapse, presence of hazardous gas whose exceeding content can have disastrous affects on workmen and high temperatures.
Our project solves the problem of detection of hazardous gases and exceeding temperature, thus providing a safety alarm system that can be used as a safety measure in coal mines. Thus our motivation strives from the present day’s innovative technology that involves robotic applications for making lives more comfortable and safe.
LITERATURE SURVEY
In coal mining—particularly underground coal mining—there are numerous conditions that can threaten the health and safety of the miners. For this reason, coal mining worldwide is heavily regulated through health and safety laws. Through the development of new equipment for personnel protection, new approaches to mine design, more effective emergency preparedness plans and procedures, and major changes in legislation, regulation, and enforcement, higher standards of heath and safety are now achieved.
The staggering data reveals that huge number of accidents occur in a coal mine during and after a disaster. The main reasons being, gas accidents, caving, flood, etc. This really asks for the development of a system that can help minimize the human and material loss that happens during rescue operations. Gas explosion is the most serious one in all mine disasters for after the gas explosion, the scene becomes extremely complex . Thus gas sensors are mandatory in the robot to be deployed.
The idea of a Mobile Robot to be able to aid the rescue team entering into a coal mine got picked up with the tremendous uplift in the field of technology. The Robot is used to reach the disaster zone and it is used for rescue and research operations. The robot can go into explosion environment and detect gas contents, temperature, etc. The data can be sent to controller in safe field. The robot is designed in such a way that it suits the mine tunnel. It can run in explosion environment, climb over ruins, check gas and if needed, slot can be provided wherein it can carry food and first aid kit to the workers trapped inside.
A biped robot was initially tipped to be used in the coal mines which can move inside the tunnel and has an RS 232 cable for interfacing. The robot couldn’t transverse a long distance it tripped on moving across the debris and the RS 232 cables couldn’t be used for a long distance. Thus a different mode of legs had to be used and after research, the usage of a conveyor belt type robot was developed. The conveyor belt as seen on the military tanks would manoeuvre over debris and rough terrains.
Now, the focus was onto the means of communication to transfer data and commands to and fro from computer and robot. In the earlier days, the robot had RS 232 cables to provide communication between the robot and the CPU. The RS-232 as the interface for communication and control to allow the robot to receive demands from the user and track objects autonomously. Though the RS 232 gave creditable communication, it had several short comings. Due to its limited size, the robot was not able to move deep into the mine. And there was the danger of the cables getting twinned or cut inside the tunnel resulting in loss of data or at times, it can spark a fire inside the tunnel. A better way of communication had to be used.
The advancement in technology saw the usage of Bluetooth for wireless communication . The mobile robot has the capability to move around autonomously using complicated and powerful algorithm. The algorithms are stored in a PC that acts as a master cum server. All sensor readings from the mobile robot will be transmitted to the master and processed. Then, command or instruction for further action is transmitted from the server to the mobile robot in a bidirectional full duplex communication mode. Hence, the main "brain" is in the server instead of the mobile robot. This again had the shortcoming of limited coverage area. The Bluetooth would function only to a specified area and the robot couldn’t be controlled beyond that.
This lead to the usage of much wide wireless communications technologies like RF transceiver and ZigBee. The ZigBee had much better range than Blue Tooth and hence it could transmit commands and receive data from long distance from the tunnel.
Once the communication and movement and sensing of robot was finalized, the focus shifted on how to make it more reliable. The idea to use a camera on the robot helps in getting live feed of what is happening inside the tunnel and it will help the rescue team to follow the less dangerous path. i.e, it helps in mapping of the mine. Robot wireless sensor networks are an increasingly capable platform and show great potential in environments from future battlefields to disaster discovery. Robot wireless sensor networks can enhance multimedia surveillance and provide the foundation for strategies based on multi-modal sensor integration .
The IEEE paper authored by Shan Cai, Zhao-long, Xu Jie, Yang Xiao-zhi Liu et al concerns a robot system fit for detecting mine disaster information on the basis of the working principle of detecting robot system. It introduces in details the structure of the system; the technologies of passing through obstacles, obstacles avoidance by using sensors; the collection of information and wireless transmission modules, including gas sensors, temperature sensors, network cameras and wireless transmission modules.
PROBLEM SUBSTITUTION
There have been various efforts made throughout the years in order to facilitate safety measures in coal mining activities. In the past, sensors were fixed at various places in the mine region, showing the levels of toxic contents and temperature readings. These however needed constant monitoring as they did not have an alarming system. Later, alarming systemwere also added to the invention in order to alarm the facilities.
These stationary sensors were not much reliable in several cases as the gas leakage and temperature exceedence are random experiences and may occur anywhere within the mining region. In such a case, the stationary sensors provide limited security. Our project addresses these problems by including a mobile alarming system controlled by wireless communication system. Our robot mounts a gas sensor and temperature sensor and moves in the mining region thus providing a complete monitoring of the region.
Although there were attempts in the past to implement such mobile robot using RF communication, there was another problem of limited area coverage. The early experiments made use of Bluetooth technology for communication between transmitter and receiver which only gives coverage of limited area (up to 10 meters). Our project provides a solution to this limited area coverage by implementing Zigbee technology for wireless communication between transmitter and receiver. Zigbee technology provides wider area coverage as compared to Bluetooth (up to 100 meters).
Further more, our project also includes a camera for monitoring of the region which gives an additional security feature of observing accidents or suspected hazardous activities in the region. Thus our project is an advanced version of security alarming system addressing all the problems faced in the earlier systems.
Complete Solution
Chat with our Experts
Want to contact us directly? No Problem. We are always here for you
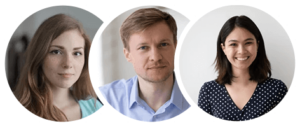
Get Online
Assignment Help Services